Helical Serrated fin tubes are produced by helically wrapping continuous serrated fin strip on edge around the tubes (pipes) circumference and continuously welding the fin strip to the tube.
Before being formed around the tube, the fin strip is cut (or "serrated") crosswise from one edge (which will become the outer edge of the fin segments) to within 1/4" of the other edge, leaving an uncut portion that will become a continuous base for the fin segments.
The interval between cuts (which determines the segment width after the strip is formed around the tube) may be specified as either 5/32" or 5/16".
After being cut, the fin strip is held under tension and confined laterally as it is formed around the tube, thereby ensuring forceful contact with the tubes (pipes) surface. 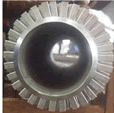
As the fin strip is formed around the tubes (pipes) its outer (serrated) edge spreads, opening the segments like petals of a daisy. A continuous weld is applied at the point where the fin strip first begins to bend around the tubes (pipes) diameter, using the gas metal arc welding process.
This welded steel fin tubes (pipes) configuration can be used for practically any heat transfer application, and is particularly suited to high temperature, high pressure applications. The important features of this configuration are efficient, effective bond of fin to tubes (pipes) under all conditions of temperature and pressure, and ability to withstand high fin-side temperatures.
manufacturing capabilities for helical serrated finned tube:
core tubes (pipes) outside diameter: 15.875mm~273mm
Fin distance: 3mm~30mm
fin thickness: 0.4mm~3mm 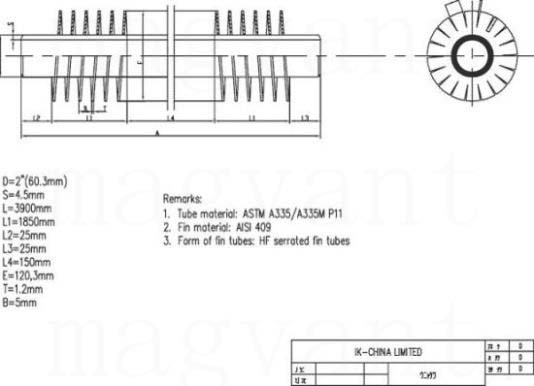 |